10 Years Strong: A Decade of Composites Innovation at Harper Engineering's Kent Facility
Published on: June 26, 2025
Harper Engineering's Kent facility marks 10 years of innovation, evolving from a bold idea into a leader in lightweight composite parts for next-gen aircraft. This milestone reflects a decade of breakthroughs, dedication, and forward-thinking engineering.
In June of 2015, Harper Engineering shipped its first composite part from the newly launched Kent facility. While small in size compared to our Renton headquarters, this facility has made a great impact—not just on our product capabilities, but on our culture of innovation. Ten years later, it's more than a milestone. It's a moment to reflect on what bold thinking, persistent problem-solving, and a few visionary decisions can do.
"Why are you putting a metal cover on a composite aircraft?" That simple question from our founder, Walt Cook, during a customer meeting sparked a chain of innovation that still drives us today.
The Spark That Started It All
Our composites journey didn't begin in Kent. Nearly two decades ago, Harper began developing lightweight solutions for aircraft interiors using carbon fiber and honeycomb structures. But the turning point came when Boeing challenged us to rethink material compatibility for their composite aircraft platforms. The result? The first carbon/honeycomb latch cover—and eventually, a need for a dedicated space to take the technology further.
Launching a second facility was no small move. For over 45 years, Harper had operated from a single location. The Kent facility represented both an operational leap and a mindset shift. Suddenly, we were not just expanding—we were building something entirely new.
"Having two facilities brought up challenges we'd never faced before. But it also forced us to grow faster, smarter, and more collaboratively."
Building Something From Scratch
Setting up a composite manufacturing line wasn't just a matter of adding equipment. Our transition from thermoset to thermoplastic materials meant rethinking everything—from processing chemistries to press systems and bonding methods.
One of the major breakthroughs came with the installation of our advanced press system—equipped with a rapid shuttle and capable of forming high-performance thermoplastic sheets with precision. We also developed a fully robotic adhesive bonding operation from the ground up.
"Many manufacturers can do reinforced thermoplastics. Our niche? We do it thin—and we do it fast."
Products That Fly—and Make a Difference
The Kent facility's first output was steel tooling for the HC-1004 latch cover. Today, we've delivered over 160,000 composite covers, including our flagship HC-1028 family for the Boeing 787 Dreamliner.
Each set of Harper composite covers saves approximately 100 lbs. per aircraft. That adds up quickly in an industry where every ounce matters—for both fuel savings and emissions reductions.
We've also begun supporting EVTOL (electric vertical takeoff and landing) programs, signaling a move into the aerospace technologies of the future.
"We're proud to be part of tomorrow's flight, today—whether it's commercial airliners or emerging electric aircraft."
People Behind the Process
The success of the Kent site isn't just about tooling and testing. It's about people—engineers, operators, technicians—who show up every day to push the boundaries of what composites can do.
Leaders like Val Khlevnoy, Tom Egbert, Oleksii Kytaiev, and Ryan Funk were instrumental in bringing the facility to life. From the first press installation to today's streamlined, high-output workflows, the pride is visible in every part that leaves the floor.
"One of our proudest moments? Watching the press make its first part—perfectly."
What many don't see is the meticulous attention to detail behind the scenes. Forming tools are cleaned daily. Fixtures are constantly upgraded. Processes are refined continuously, all to deliver the consistency and quality our customers expect.
Looking Ahead: Innovation in Motion
The next decade holds even more promise. We're currently collaborating with a major composite materials supplier on a new project to develop fully thermoplastic sandwich panels—no adhesives, no secondary bonding. Test parts are expected this fall, with a full demonstrator targeted for early 2026.
We also plan to expand our use of hybrid overmolding, a process that successfully bonds injected thermoplastic resin to reinforced substrates. It's fast, strong, and ready for production.
"This isn't just about new parts. It's about new ways to think, build, and fly."
Celebrating 10 Years—and Looking to the Future
From a single latch cover to next-gen thermoplastic assemblies, Harper's Kent facility has become a symbol of what's possible when engineering meets perseverance.
Here's to the next ten years of curiosity, capability, and composites.
Photos:
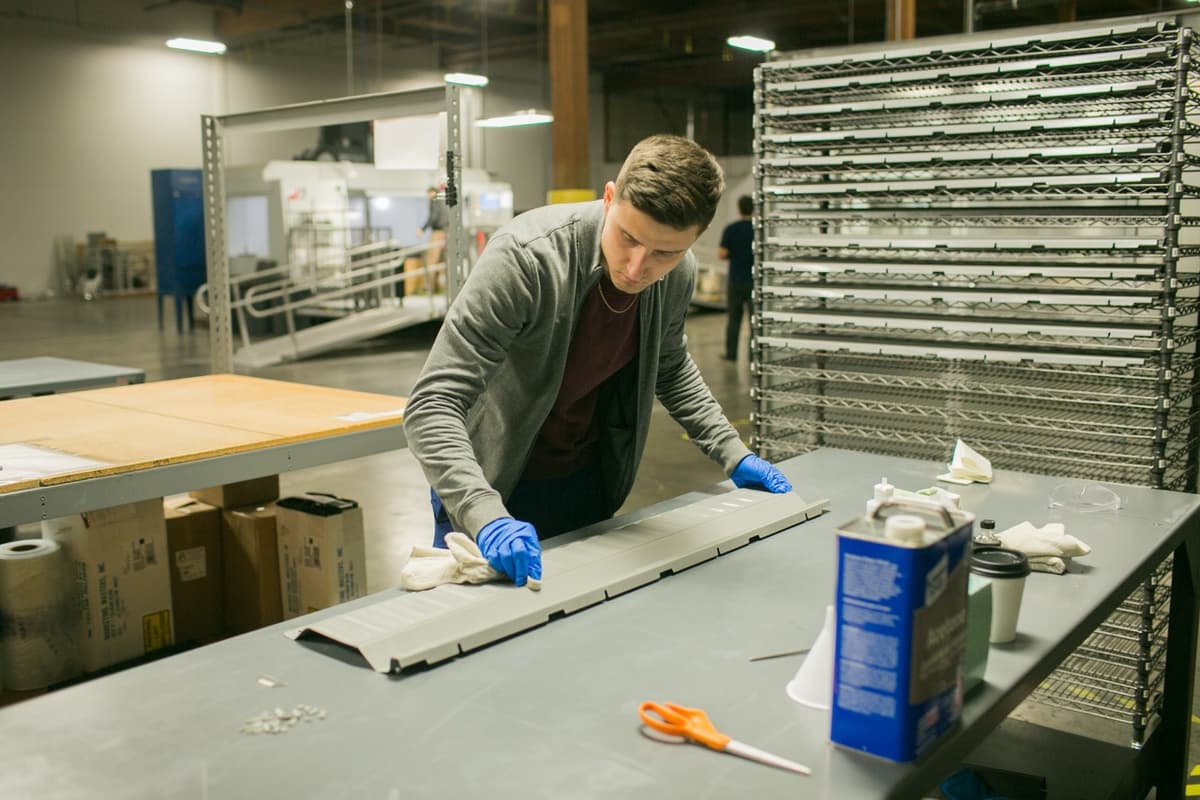
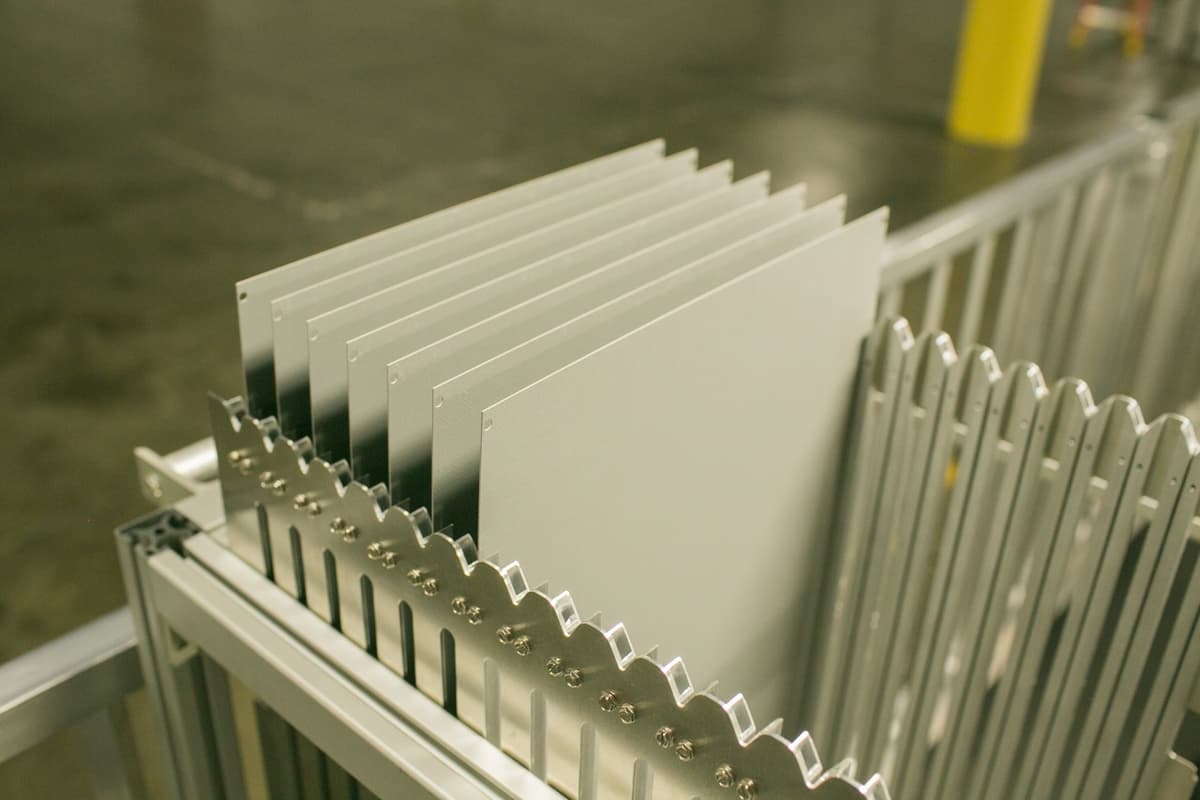
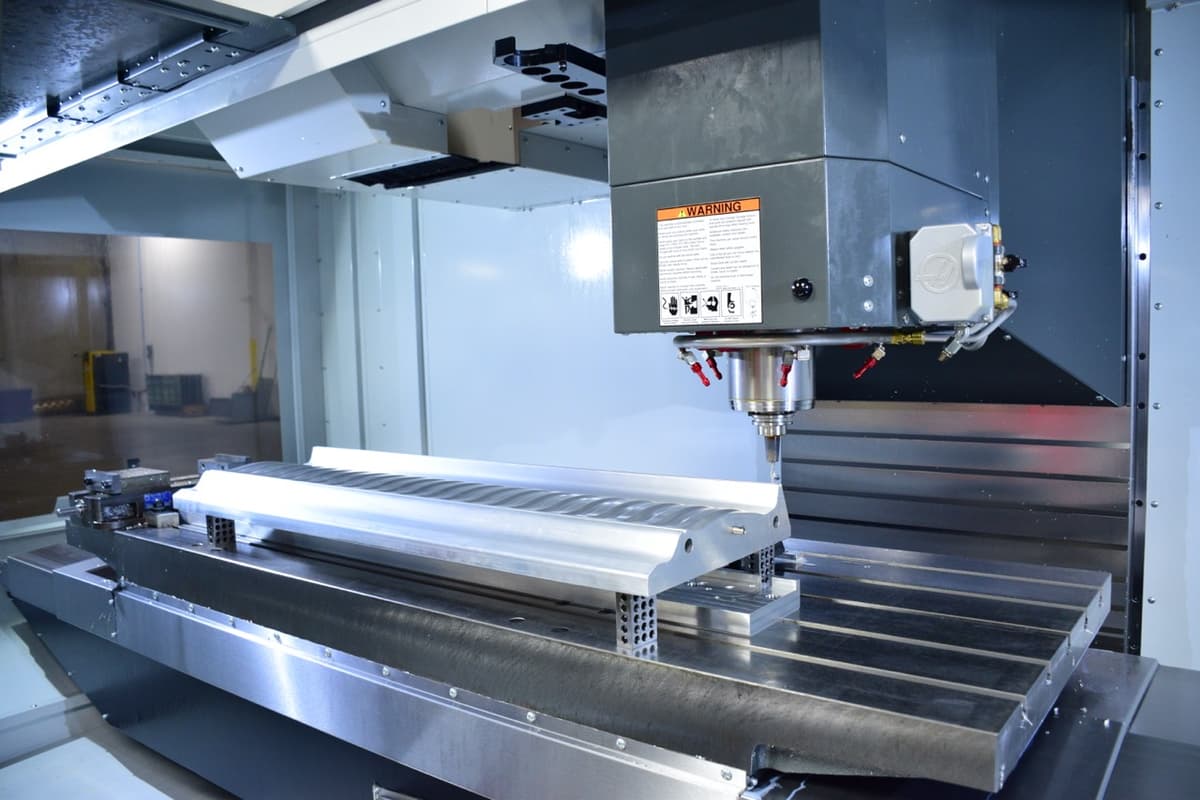
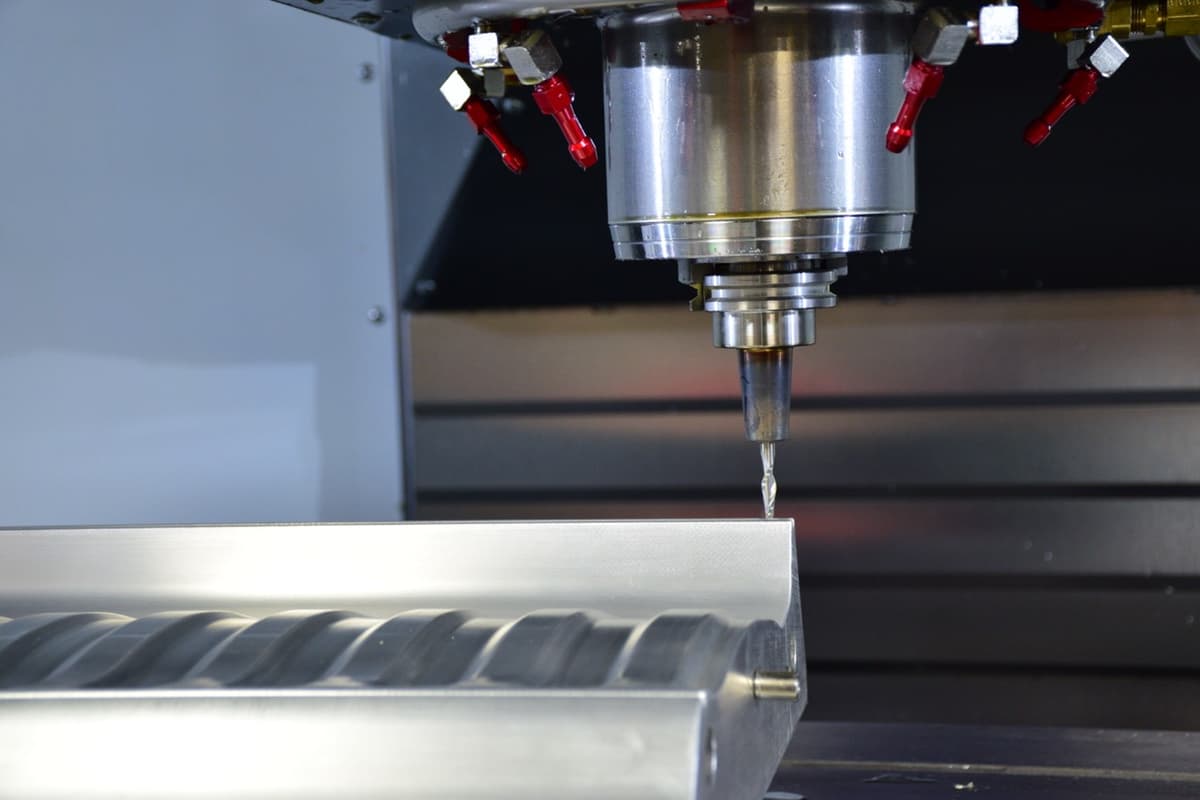
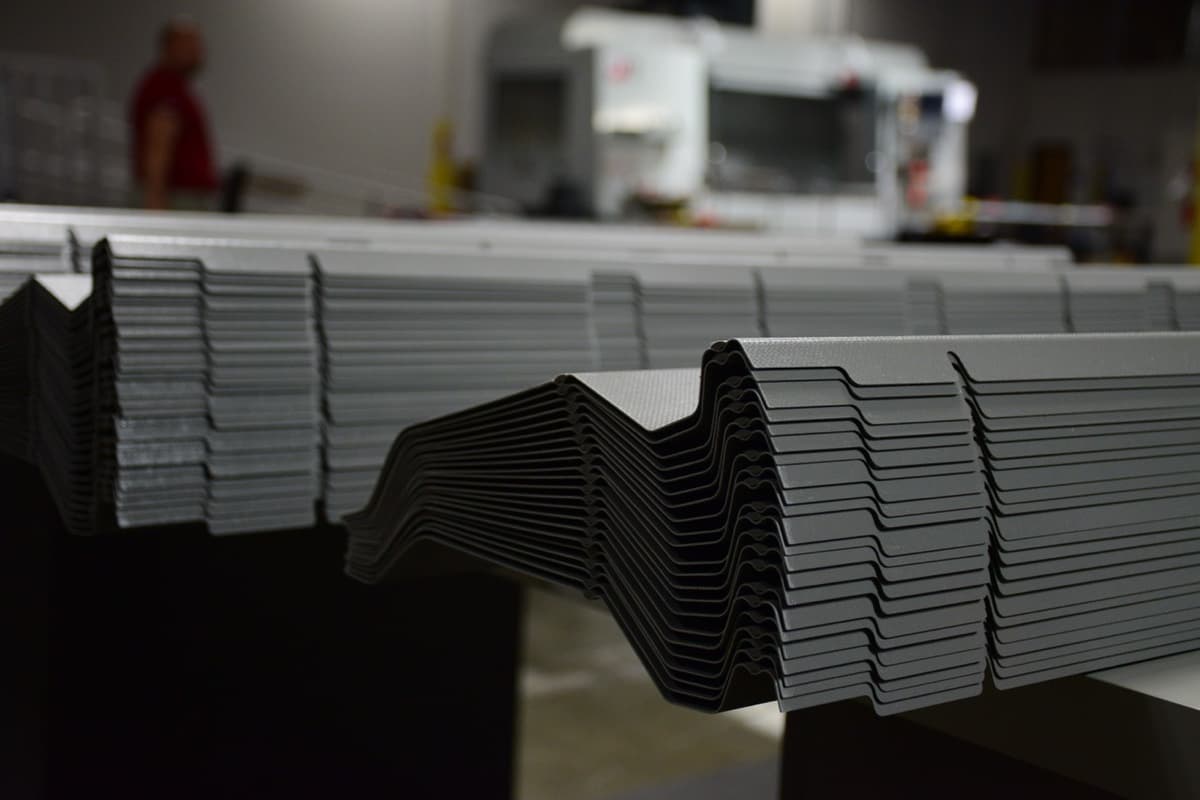
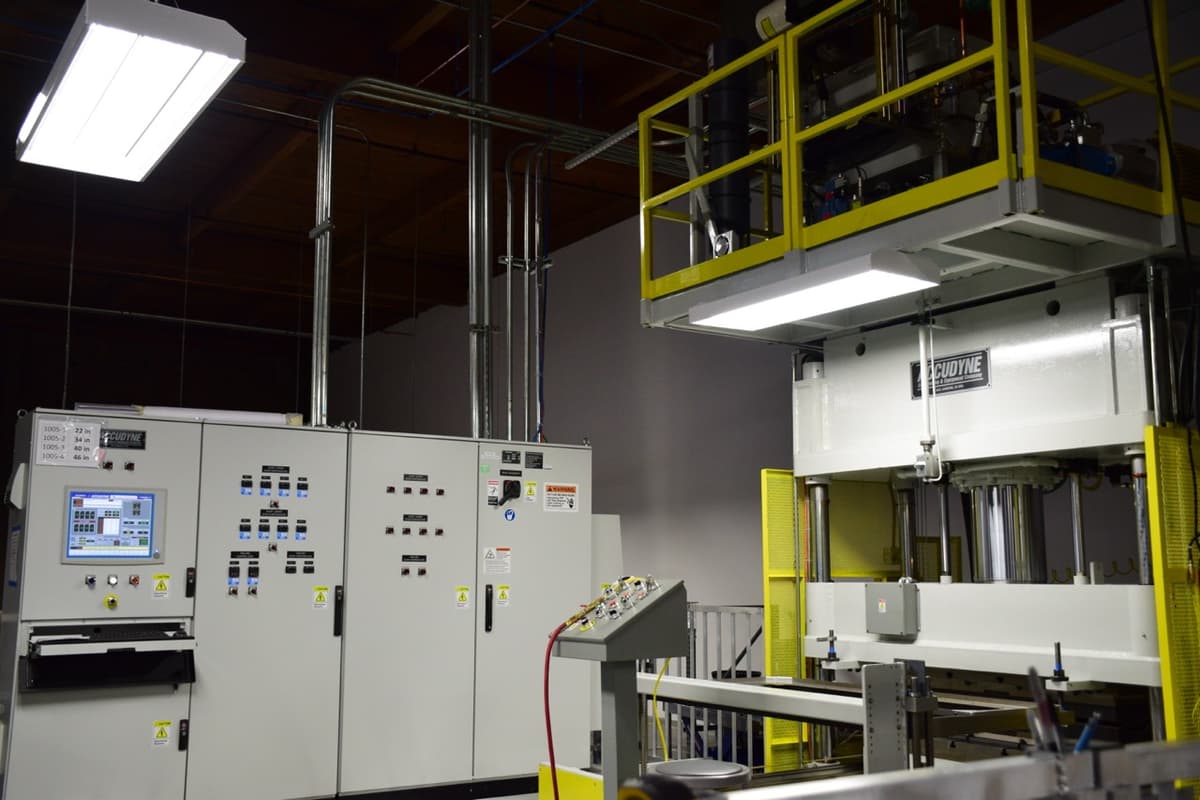
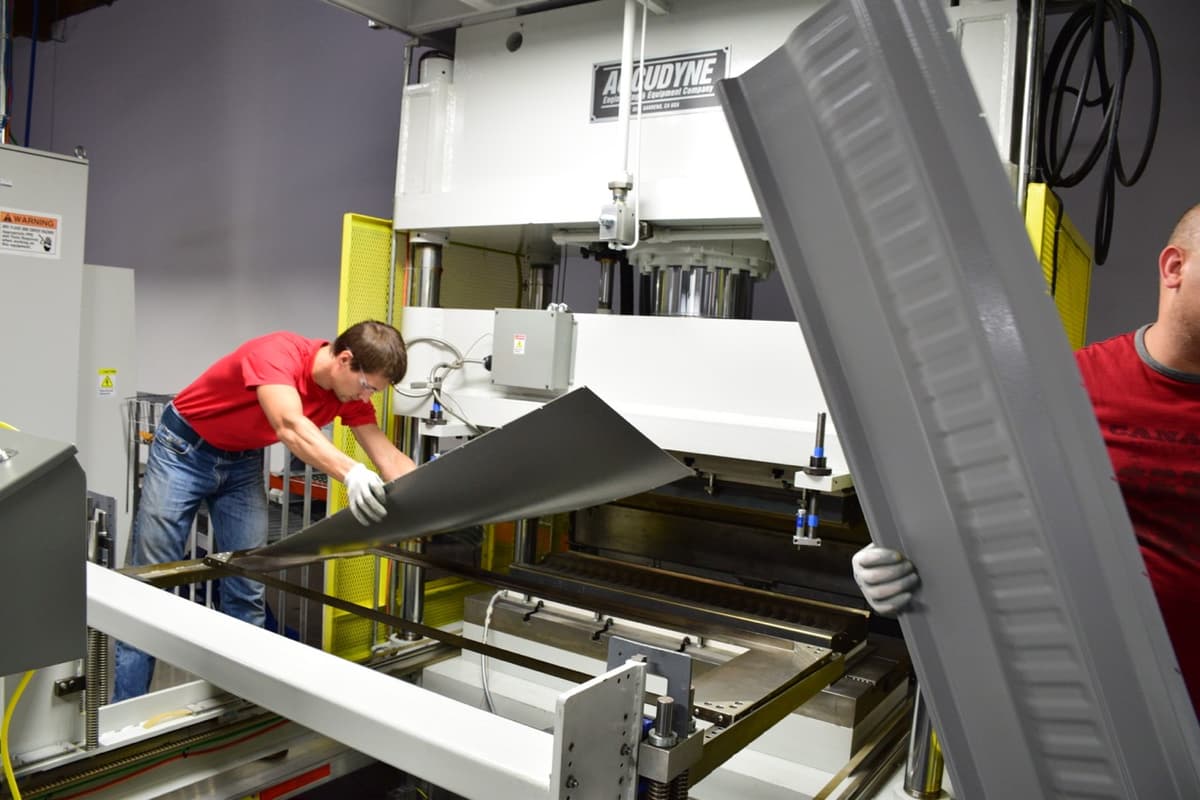
About Harper Engineering Co.
Harper Engineering is a leading provider of innovative solutions for the aerospace industry, specializing in precision engineering, manufacturing, and sustainability. With a commitment to excellence and environmental responsibility, Harper Engineering delivers cutting-edge products and services that meet the evolving needs of the aerospace sector.